케이스..케이스..케이스..
on
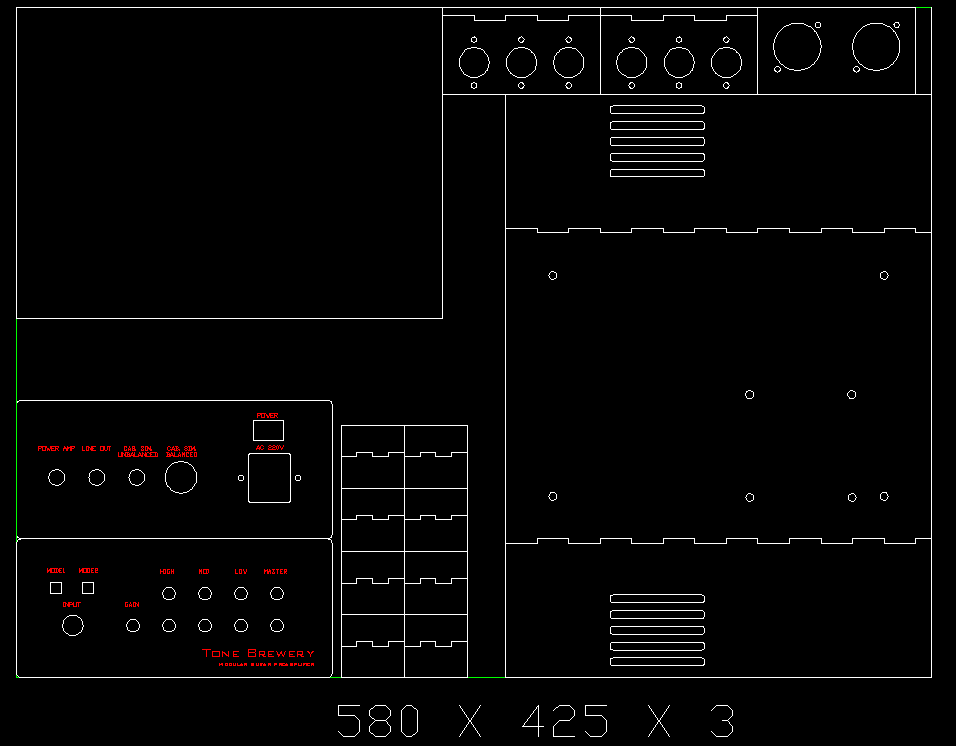
케이스를 만들기 위해 캐드작업을 해봤다..
크기는 200 X 88 X 270이 적당한 것으로 계산됐다.
높이가 88mm인 것은 1U size가 44mm라서 2U size를 감안한 것이다. 5mm 아크릴을 생각하면 내부 공간의 최대 높이는 78mm 정도가 된다.
이는 85.8 core 트랜스가 간신히 들어설 수 있는 높이이며 76 core 트랜스는 다소 여유가 있다.
맘이 슬슬 바뀌어서 TB1(1호기 프리앰프를 그렇게 부르기로 했다)에 들어있던 트랜스를 TB2에 쓰고 새로 주문한 76 core 트랜스를 12V 전원을 쓰지 않는 TB1에 넣을까 생각 중이다. 그러면 전원부를 다시 만들어야 되는데, 어찌되었든 12볼트 전원은 메인보드에 만들어 넣어야 한다.
캐드질은 눈 대중으로 대충 드릴질을 하고 줄질을 하는 것과는 매우 다르다.. 부품의 사이즈를 정확히 알아야하는 것은 기본이고, 끼워넣었을 때 여유가 있게 설계해주어야 한다. 역시 경험이 없으니 한 두번은 만들어봐야 제대로 설계할 것 같다.
일단 여기서 문제 발생..
아무리봐도 두께 3mm 짜리의 아크릴은 빈약해보인다.. 전면 패널로 쓰든 뭘로 쓰든 크기가 커지면 본래의 평평한 상태도 잘 유지하기 힘들어 보인다.. 게다가 열에 약하다..
그렇다고 금속 패널에 붙여놓으라고 만든 전자부품들을 3mm 보다 두꺼운 아크릴 판에 붙이기는 쉽지 않다. 철판이나 알루미늄판은 두께가 1mm만 되도 왠만큼의 강도를 가지고 있으니 뭘하든 상관없지만..
3T의 아크릴은 기타의 픽가드를 생각하면 된다. 대개 픽가드는 강도를 높일 목적으로 단일 아크릴로는 잘 가공을 안하는 것 같다. 내가 가진 아이바만 해도 1T짜리 아크릴 3장이 곂쳐져있다. 어쨋거나, 기타 픽가드를 생각하면 뭐 전면판넬로는 그럭 저럭 문제는 없을 것 같다.
그래서 주문 가공해주는 곳을 알아보니, 싸게 구멍을 뚫어준다는 업체에서는 기계가 고장나서 수작업을 해준다고 하는데 사실 별로 믿음직스럽지 못하다. 그렇다고, 레이져 가공을 생각하자니 200 X 88짜리 판넬 하나 가공하자고 작업을 의뢰하긴 좀 어이가 없다.
일단 5mm짜리 판 5장과 3mm판 1장을 주문할까한다. 믿음직스럽진 못하지만 수작업으로 구멍가공은 맡겨볼까 한다. 고무발 대신 장식용 나사인 다보 4개를 쓰면 좋을 것 같고, 진공관과 모듈을 갈아끼기 위한 상판은 본래 생각한대로 경첩을 두개 써서 여닫을 수 있게 만들까한다.
물론 전체적인 색깔은 스모크로 통일할 생각이다.
전원은 넉넉하니 고휘도 LED를 붙이는 것은 아무때나 가능한 일이다.
아래 그림이 캐드작업의 결과물..(오토캐드 만져본지 세시간쯤? 따라서, 수준은 상당히 허접함)